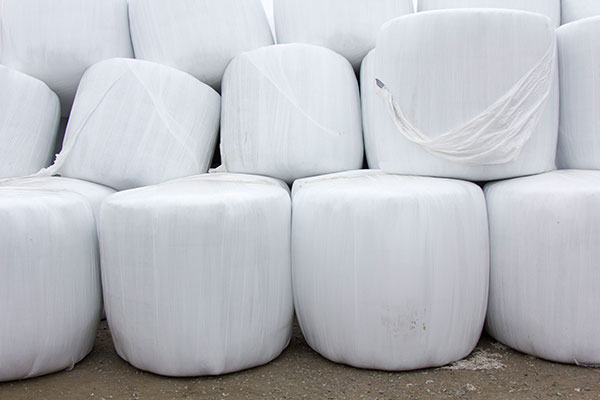
When I moved to Wisconsin in 1988, one of the things I noticed in short order was that baling hay of any size, shape, or type was a minimal, if not nonexistent summer activity on most dairy farms. This was a big change from previous locations where I had hung my cap.
Everyone chopped and ensiled haylage. Frequent rain events, high humidity, labor issues, lower quality, and mixed rations were all given as reasons why baling dry hay was just too much of a battle.
During the past 25 years or so, the baling world has melded with the chopped haylage world in the form of baleage. These days, high-moisture hay storage isn’t just a dairy thing, but has expanded into beef and other livestock enterprises; wrapped hay can be found in virtually all humid regions of the United States. Growth in this harvesting process has been pretty dramatic and weather events during this past summer likely won’t hinder its growth.
So why make baleage?
Simply put, the drying time is drastically reduced. Drying hay down to 50 to 60 percent moisture happens a whole lot quicker than getting it down to baling moisture.
Generally speaking, and especially for legume hay, the forage quality of baleage will be better than the same hay put in a dry bale. There is both reduced carbohydrate loss from respiration during wilting and less leaf loss during raking and baling. Further, the odds of getting the crop rewetted from rain are much less.
Perhaps a key advantage of baleage — one that is not initially considered — is less wastage during feedout. After incorporating baleage into a feeding program, this is often one of the first observations made, and the difference in waste can be upward of a 15 percent advantage for the high-moisture forage.
In a recent Iowa State University extension publication, Making the Switch to Baleage, authors Patrick Gunn and Joe Sellers estimated a cost savings of 33 cents per head per day for a cow-calf winter diet feeding baleage versus dry hay in a ring feeder. The advantage comes from improved forage quality, a lower supplement cost, and reduced wastage.
Making failage
Though there are many advantages to baleage when done correctly, there are some huge consequences when recommended harvest and storage practices aren’t followed. This is what I refer to as “failage,” and here are the six ways it is most often made.
Saving on wrap: The entire system hinges on oxygen exclusion for optimal fermentation. The research and farm experience is pretty conclusive that six layers of 1 millimeter (mil) plastic are needed, especially for large square bales. If you try to get by with less, you’ll pay the price. For storage longer than nine months, eight layers may be needed.
Compromised wrap integrity: There are a number of ways that bale plastic can be ripped, punctured, torn, ruptured, cut, or stuck. Sometimes it’s preventable, sometimes not. Wrapped bales, individual or in-line, need to be stored in (preferably) a prepared area where weeds can be controlled and wildlife activity is discouraged. Bales need to be monitored on a regular basis and holes patched with tape specifically made for agricultural plastic. Allowing air into the wrapped bale will cause widespread mold, boost feed wastage, and negate most of the benefits inherent with making baleage.
Too wet – too dry: Just as with any high-moisture feed, there’s a sweet spot to obtain optimal fermentation. Wayne Coblentz, USDA-ARS research scientist in Marshfield, Wis., points to that ideal moisture range being 45 to 55 percent. Forage that is drier than 45 percent moisture will not produce as many fermentation acids and have a higher pH. If drier forage is wrapped, oxygen exclusion is paramount if excessive heating and mold are to be prevented. An enhanced risk of clostridial fermentation occurs if the forage is too wet (over 60 percent moisture). This is especially true for legumes.
Air pockets: This has always been an issue with in-line wrappers, though my observation is that some producers are really good at making tight, uniform line wraps with no air gaps. The key to avoiding air pockets is to have uniformly-sized bales that snugged tight against each other. Once again, air is the enemy and a whole lot of damage can be done when air inhabits a line wrap.
Too late: Ideally, bales need wrapped within four hours of baling, but that’s often not practical or feasible. Research indicates minimal damage occurs within the first 12 hours after baling, and that should be the goal. If forage is allowed to heat before being wrapped, the buffering capacity of the feed rises and it becomes more difficult to get a good fermentation.
Loose as a goose: Dense bales wrap and preserve better. Many companies are now making round balers specifically designed with the baleage maker in mind. Forming uniform, dense bales may require a slower ground speed and higher PTO speed. Adequate moisture is also important. Aim for a bale density of 10 pounds of dry matter per square foot or more.