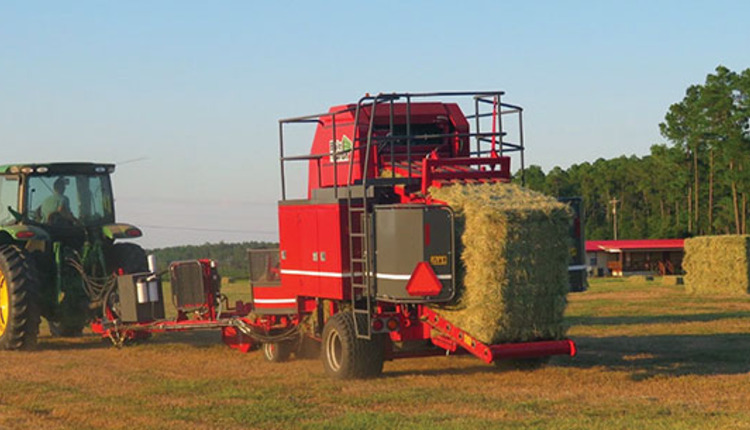
Now that winter is in full effect, most grain farmers are either ice fishing or taking a vacation at the beach, but not us hay guys. Winter is when hay producers reap the rewards of their hard work and long hours spent during the past summer.
The winter workload brought me to think several times how I could make a little more free time available for both me and my family because many of our days were spent loading truck after truck of small square bales.
These little square bales can cost you more dollars in time and labor than anything else on the farm, but they can also bring home the biggest reward if managed efficiently. That is why my family has been in the small square bale business for the last 40 years. These days there are many excellent options for handling two-tie bales.
There weren’t many good mechanical handling options for our commercial haying operation when it started back in the 1970s. Manual labor seemed to be the most popular choice and is the way I “cut my teeth” in the hay business; I started driving the truck and trailer before I could even reach the clutch pedal. There is nothing in the world wrong with this method, and quite frankly you can figure out how tough you really are in the top of a barn during the middle of July on a hot Georgia day. We rarely got much hay wet, but at the same time we were limited to about 800 bales per day.
Moving to bale wagons
Our first step to mechanical freedom was a pull-type bale wagon followed the next year by a second. These pull-type wagons hauled and stacked 105 bales per load and boosted production to over 1,500 bales per day. A few years later we made the big jump to a self-propelled stack wagon, which is still our choice in the operation today. A single wagon made it possible for one person to pick up and stack upward of 2,500 bales per day. They are efficient and effective for getting hay out of a field and into a stack. However, the barn or stack needs to be relatively close because they only haul 160 two-tie bales; too much road travel can eat into productivity.
In my opinion, one of the only weak spots for these bale wagons is during load out. The other is the price on these wagons, which has now risen to over $175,000 for a decent used unit. If you sell most of your hay retail, as we do, it usually means the only way to load the truck is manually. I know there are squeezers out there that you can grab a section of the stack and load a trailer, but not every trailer loads the same, and that method can still lead to some manual labor finishing up the loads. If getting the bales out of your field with low labor input is highest on your priority list, then bale wagons are worth consideration.
A cheaper option
Other options that have been around for decades are bale accumulators and grapples. In today’s small square market, the bale accumulator and grapple are probably the most cost-efficient way for getting started in the business. New accumulators start around $10,000 and grapples are near $4,000. There are also numerous new and used models available. The best thing about this system is you rarely need to manually handle bales. They can be loaded out of the field to a trailer and then unloaded into the barn by loaders. When the bales are ready to be sold, they can be picked up again in the same pattern by the grapples and loaded onto the trailers.
The downside is the number of pieces of extra equipment needed. To be efficient, you need two loaders, one in the field and one at the barn, with several trucks and trailers to haul the bales. It takes multiple people to really run these accumulator crews efficiently, but they can get you started at a lower cost and can be adapted to any size operation.
Bundle up
A relative newcomer to the market is the bale bundle machine. There are a few different models available and each has proven to be reliable and productive. These machines can be pulled behind the baler, pulled by a separate tractor, or purchased as self-propelled units. They wrap a strap or twine around different bundle sizes such as nine bales, 18 bales, or the most popular 21-bale bundles. The 21-bale stacks are seven bales wide and three high, stacked on edge. If you put one stack on top of another, they fit perfectly into a van trailer.
If you deliver a lot of your crop in a dry van, bale bundlers would be at the top of my list. They have quite a few moving parts and some have an onboard computer, but all have proven to hold up for hundreds of thousands of bales. They are a bit on the expensive side with new pull-type models, which can keep up with two balers, starting at around $75,000 and going up to $100,000. You still need loaders in the field and at the barn along with extra trailers for hauling. In terms of efficiency, I believe these bundlers can pay for themselves in short order.
Who knows where the two-tie bale market will be in the next 40 years. Maybe we all will be using big square balers that can make smaller packages. Or maybe we will still be using the same bales that have been around since the 1930s, as they are the preferred package of many horse owners when feeding their most treasured companion.
This article appeared in the January 2017 issue of Hay & Forage Grower on page 18.
Not a subscriber? Click to get the print magazine.