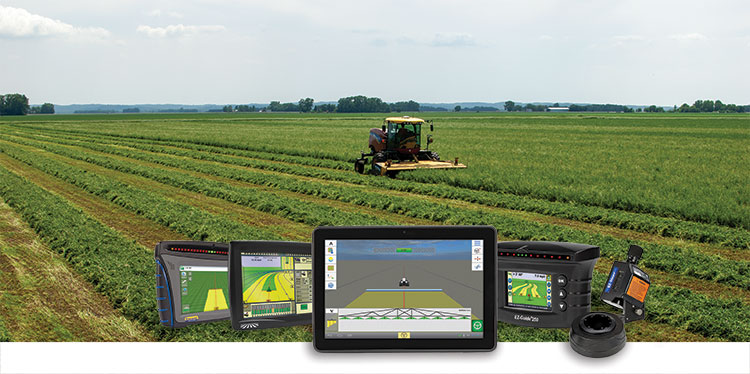
Last season was a challenging one for hay production. Wet weather pushed growers to cut hay later than desired, diminishing forage quality and yields. The season served as a reminder that although we can’t control the weather, there are things we can do. When difficult conditions persist, leveraging technology can play an important role in minimizing negative impacts.
Precision farming technology can help maximize hay yields while alleviating stress on you, your operation, and your haymaking equipment. Simple, easy-to-use tech additions to new and older equipment can help haymakers maximize efficiency and reduce other variables like fuel costs and time. Other accessories and equipment designs can help you get back into the field faster.
Efficient cutting
It all starts with cutting, conditioning, and swathing. It’s important to achieve the proper forage cut and conditioning, especially when weather conditions play a factor. Raise cutting heights and take advantage of wide conditioning systems for fast dry down. Aftermarket fixed and adjustable dealer-installed skids are available to help boost cutting heights and lower the risk for high forage ash content. A variety of blade angles are available to help ensure a clean cut and even finish.
To protect your mower and crop, hydraulically controlled blade height lets you tip back in rocky conditions. A dealer-installed hydraulic tilt kit with more adjustments is available for many older models. In thick and wet crops, accessory disc lifter kits and replacement wearing parts are recommended to smooth crop feeding.
To cut as efficiently as possible, a variety of easy-to-use technologies are available. Simple and affordable, a light bar display provides haymakers with an entry level guidance solution. Assisted steering guidance systems are the next level of performance. They reduce manual steering and improve cutting accuracy. This allows the operator to focus on the task at hand, which is frequently behind the tractor, significantly reducing operator fatigue while improving productivity and work quality.
Besides reducing operator fatigue, these systems improve efficiency throughout the haymaking process. Even less skilled operators can produce more consistent, evenly dried, parallel swaths that are easier to ted, rake, and bale. Today’s aftermarket assisted steering and guidance systems are easy to retrofit to older tractor models and are simpler to operate and less costly than previous versions.
Watch the water
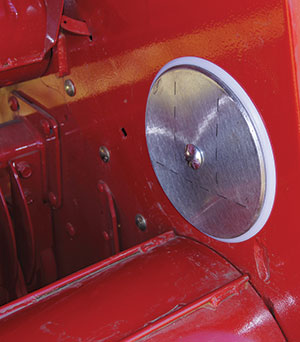
Make the most of short weather windows with a hay preservative system. A hay preservative allows baling at a higher moisture level while lowering the risk for heating and spoilage. Hay preservatives maintain the hay’s green color, are safe for livestock, and won’t corrode machines. Choose an easy-to-use manual system or the more advanced automatic applicator.
Baler tech
Unlock the potential to work faster and easier with baling automation. When it comes to round baling, the full-bale alarm can be annoying with multiple hours in the cab. The latest ISOBUS-equipped round balers can take the stress out of operation by automatically stopping the baler, tying, ejecting, then closing the tailgate for you.
When lower cost per bale and higher forage quality matters, a dense bale is a must. A recent Penn State University study confirmed higher density silage round bales retain greater forage quality by excluding more oxygen during the fermentation process, keeping bale temperatures cooler. This prevents heat binding of proteins, making more protein available while also extending ring-feeding time. It also means fewer bales per acre, lowering bale tying, film wrapping, and handling costs. You can adjust bale density for the crop and moisture. For convenience, the latest round balers are available with in-cab bale density controls.
When the weather is right and it’s time to bale, uptime and reliability are essential. Aftermarket chain oiling and automatic greasing systems reduce periodic maintenance to save time and ensure your equipment is ready to roll. Take advantage of dealer-installed accessory kits for many older and late-model round balers.
A winter upgrade to endless belts will help ensure trouble-free performance throughout the season. Alternatively, stock belt lacing kits for when you need them. You can improve performance when baling higher moisture crops with aftermarket round baler performance kits. In difficult conditions, roll scraper and tailgate chopping roll kits improve uptime.
Whether you choose a high-tech or low-tech solution, many new technologies and aftermarket tools are available to help you maximize your efforts. Start by accepting the things you cannot control, then take the right steps to influence those you can. A variety of nondigital and technology tools are available to help optimize forage quality so you can maximize your haymaking return on investment.
- Cut as efficiently as possible. Even with older equipment, choose an easy-to-use and affordable light bar display. Assisted steering guidance systems are the next level of performance.
- Raise the cutting height to reduce forage ash content. A variety of blade angles are available from your dealer to help ensure a clean cut and even finish.
- Lay it wide and update or replace worn cutting parts. A cleaner cut boosts harvested yield. Smooth feeding enhances conditioning. Wide swath for fast crop dry down.
- On-board moisture sensors give you accurate and real-time data, so you know when to bale or move on to another row. This will help maximize forage nutritional content.
- Crop preservative systems let you bale at higher moisture levels while also preventing heating and spoilage. Both manual and automated systems are available.
- Boost bale density to lower your cost per bale and retain higher forage quality. Higher bale density improves baleage fermentation, extends feeding time, and lowers per bale cost.
- Replace your baler belts during the winter months. Choose endless belts for reliability and to produce a uniform, high-density bale that maximizes nutritional value.
- Use only high-quality net and film wrap to keep bales densely packed and protected from the elements, locking in nutritional value.
- Reduce periodic maintenance with aftermarket chain oiling and automatic greasing systems that help save time and ensure equipment is ready to roll.
- Take advantage of aftermarket performance kits to improve operating efficiency.
This article appeared in the January 2020 issue of Hay & Forage Grower on pages 20 and 21.
Not a subscriber? Click to get the print magazine.