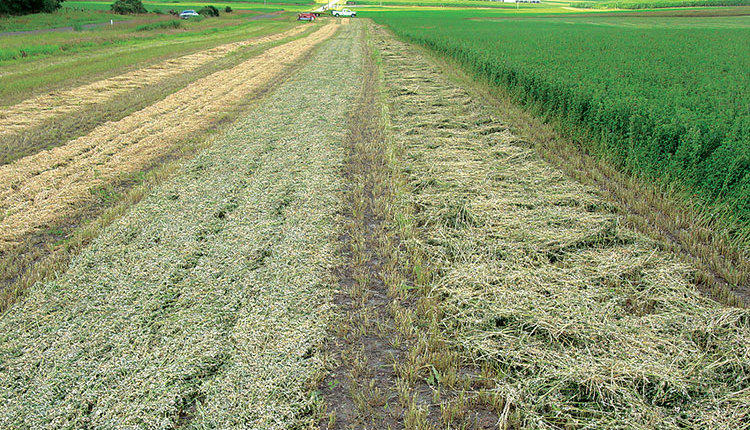
Rapidly drying hay and forage to the desired moisture for safe conservation is both challenging and frustrating. Productive and efficient cutting equipment, rapid field drying, and timely harvest with cooperative weather are all needed to achieve a high-quality forage.
Rapid drying to harvest moisture is most effectively accomplished by placing the crop in as wide of a swath as possible and by properly conditioning the crop to reduce the resistance of moisture leaving the plant. In the end, weather conditions will drive success or failure. The future of haymaking is understanding and managing this risk with decision-making tools that harness public and on-machine data.
Depending upon yield and initial moisture, between 1,000 and 1,500 gallons of water must be evaporated per acre to get the crop ready for chopping at 65% moisture. To evaporate that much water, water vapor must exit either through the leaf stomata or by diffusion through the stem’s waxy cuticle. Moisture movement through open stomata is faster than through the cuticle.
Right after cutting, the leaf stomata are open, promoting rapid water loss. However, research has shown that water vapor movement from the leaf stomata dropped dramatically within 15 to 30 minutes of cutting, and that 70% to 80% of the stem moisture remains when stomata close. When the stomata close shortly after cutting, the rate of moisture loss rapidly declines as water vapor must leave through the stem’s waxy cutin. This is why mechanically conditioning to split or break the cuticle is so important to provide faster drying.
Always dried faster
Conditioning at cutting is widely practiced, yet the benefits are seldom fully understood. Our research group has conducted many alfalfa drying studies over the last several decades. We often will include an unconditioned control treatment. When swath width and formation were similar, conditioning always resulted in faster drying (see Figure 1). This is true whether the intended harvest practice is haylage, baleage, or dry hay. Simply put, conditioning forage crops always resulted in shorter field drying time, even to haylage moisture.
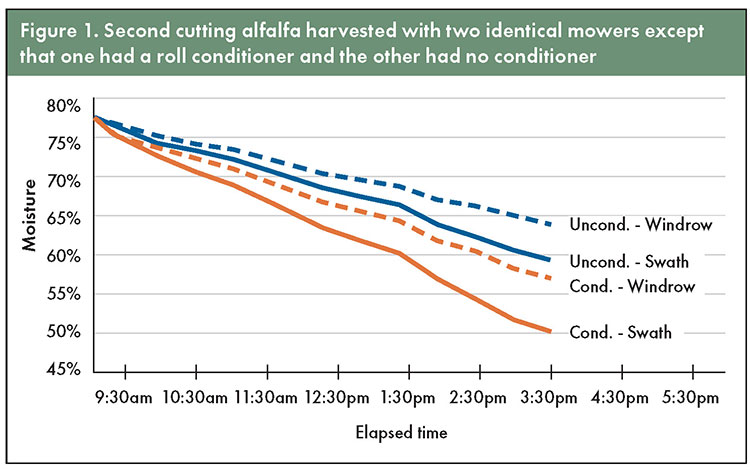
Conditioners will crack, crush, or abrade the stem so the resistance to water movement is reduced by breaks in the stem epidermis. Crimping rolls pass the crop between intermeshing, noncontacting rolls, which bend and crack the stem at intervals. Crushing rolls pass the crop through intermeshing rolls with small clearances, intermittently flattening the stem. Impeller conditioners use rotating fingers to abrade the stems. Comparisons between impeller and roll conditioners have shown that roll conditioners produce faster alfalfa drying while impeller conditioners create faster drying of grasses.
After conditioning, the most effective way to get a crop to dry faster is to place the crop in wide swaths. Laying the crop in a wide swath allows the drying crop to capture more of the solar energy, which raises the plant’s temperature to evaporate internal water. The sun’s energy increases the air’s water-holding capacity so the air surrounding the plant is less humid. Wide, uniform swaths also promote more air exchange around the plant, helping to reduce the chances of stagnant, humid air surrounding the drying plant.
The ultimate in wide swath drying is tedding the crop after a short period of wilting. Tedding not only spreads the crop to cover the whole field but mixes and fluffs the crop, which promotes air movement. More producers are using tedders, even when making haylage, to reach chopping moisture sooner.
Modeling provides promise
Regardless of following best practices for haymaking, rapidly changing weather conditions continue to impair our ability to maximize hay quality. Consequently, the next frontier in haymaking is predictive modeling of crop development and drying rates. These models will combine multiple data sources such as remote and on-machine sensing with crop growth rate, drying, and weather models.
With predictive modeling, the goal is to provide a haymaking forecast. These forecasts would allow producers to perform what-if scenarios such as:
What if I cut today?
What if I tedded the crop?
How would raking the crop influence time to baling?
In addition to scheduling and what-if scenarios, the system would alert the producer of changing conditions. As a result, these systems might suggest an intervention such as tedding, raking, or use of a preservative. Ultimately, the goal is to enable the producer to evaluate the trade-offs between missing the optimal crop maturity and weather risk, thus improving the margins in hay production.
Parting thoughts
Finally, keep these practical mowing and conditioning considerations in mind:
- The purchase price of a triple mower will be about 25% less without conditioners.
- Conditioners add to repair and maintenance costs and will require more fuel per acre when mowing.
- A longer harvest window at the desired moisture may result from not conditioning but at the risk of longer wilting duration to reach that moisture.
- Drying to baleage moisture (45% to 55%) will be much more difficult without conditioning. Getting forage to dry to hay moisture will be very difficult without conditioning.
- Chopping cover crops such as ryelage is becoming more common. Conditioning helps moisture move from these thick-stemmed, slow-drying crops.
- When there is no conditioner, the stems tend to lay aligned with the direction of travel. This can lead to losses when merging because the pick-up teeth easily rake through the aligned stems. Cutting at a slight angle of 2 to 3 degrees can alleviate this problem, but this is not always an option in fields that are on the contour or irregularly shaped.
This article appeared in the April/May 2021 issue of Hay & Forage Grower on pages 16 and 17.
Not a subscriber? Click to get the print magazine.